We use cookies to give you the best possible experience. To accept cookies continue browsing, or view our Cookies Policy to find out more.
The Ultimate Guide To Cotton Fabric Manufacturing: Part 6 - The Product Makeup Process For Bedding & Towels
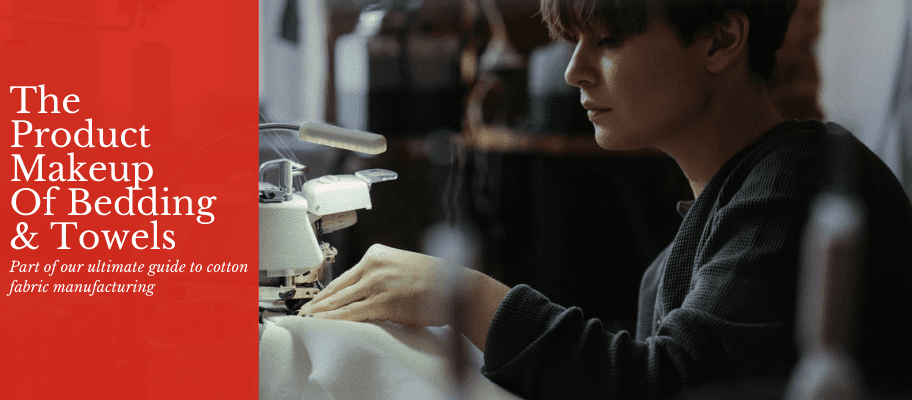
Now that the finishing touches have been added to the material (read about that in part 5) and the fabric has been given all the treatments it needs to make it fit for use, it’s time to make it up into the final product. In this part we’ll cover the product makeup of bed and bath linen, including the process that turns it into the final product.
How is Bedding Made?
Firstly, the finished fabric is laid out in layers on a long table. It is then cut according to a set plan. This basic plan includes a calculation of how many bed sheets, duvet covers, and pillowcases are going to be cut and what size they need to be. Here, the faults are also removed or tagged.
When it comes to bedding, particularly duvet covers and pillowcases, it’s especially important that the top and bottom pieces are cut from the same batch of fabric. If the product was from different batches, the two fabrics may shrink to different levels or one fabric may be slightly more skewed than the other. This means that when the duvet cover or pillowcase is washed, the shape will distort as the different pieces shrink. This leaves you with a useless piece of bed linen!
Finally, it’s also particularly important that the top and bottom are cut from the same fabric direction. This is done because the fabric will always shrink more in the warp or lengthways direction when washed. The reason for this is because the fabric has been constantly pulled and stretched through the various stages of processing. So, when it’s finally washed, the fabric relaxes and shrinks back in length. The weft or width will also shrink, but not to the extent that the length shrinks. This is because it hasn’t been stretched to the same amount as the length has.
So, if the top of a pillowcase is cut lengthways from the fabric and the bottom is cut width ways, the top will shrink more and the pillowcase will twist when its washed, making it exceedingly difficult to iron. The same happens with a duvet cover, as you’ll end up with a diagonal crease across it.
To sum up, in the case of 2 ply products such as duvet covers and pillowcases, it has the following benefits if each ply is taken from the same cut piece of fabric:
- The same level of bow/skew and shrinkage.
- It’s less likely to distort when laundered.
When each ply is cut from the same fabric direction (warp or weft) it has the following benefits:
- The same shrinkage levels.
- Prevents twisting upon laundering.
Next comes the stitching stage.
Stitching Bed Linen
The next sage is stitching the fabrics together to make the final product. This stitching process is known as hemming. In hemming the edge of a piece of fabric is folded and sewn. This is done to prevent the separating of the fabric and to adjust the length of the final product. Hemming is traditionally done on manual sewing machines, but automatic hemming machines are becoming increasingly common. However, automatic hemming machines are awfully expensive to buy, so the factory must make a careful choice depending on how quickly they can make their money back.
Now we've covered bedding, let's move on to towels.
How Are Towels Made?
Towels have cutting lines woven in as part of the overall pattern, which separates the weave in the individual towels.
The fabric is first cut along the woven in lines in the length, which is done automatically by a machine. This process gives a single towel width strip. The towel strip is then cut across the width after the side hems have been stitched, which is again done by a machine or, increasingly less common, by hand.
Stitching Towels – Side Hems & Top Hems
The strip we got from the cutting process is then hemmed down the sides using a twin or double stitch.
At the side of the towel there is an area that has been woven with no pile and features the plain ground weave. This area is folded under then folded again by the machine. This is followed by twin needles sewing a double stitch that passes through both of the folds. This twin stitch process gives extra hold and a strong hem.
One issue with towels is that the hems can start to fray and come apart after the towel has been washed. This can happen when the pile of the towel falls over on to the area to be hemmed. To solve this, the needles are guided by a laser, which detects the pile and makes sure the stitch doesn’t sew through the pile by moving the needles further away to the side.
However, if the pile is too close to the stitch path, this creates a problem where the needle can miss or only just catch the folds in the hem. This results in an extremely weak hem that will fail after only a few washes. This is why a twin stitch is carried out, as doing only a single stitch that misses the middle fold creates a much higher chance that the hem will be weak, eventually fraying and coming undone.
Finally, the hemmed strip of towels is cut across the width into individual towels that are normally sewn by hand.
At the end of all this, you should have some quality bedding or bath linen that’s ready to sell and deliver to customers.
This concludes the product makeup section of cotton fabric manufacturing process and the ultimate guide. Don’t forget, you can view previous parts in this guide by following the links below:
Read Part One - The Harvesting and Cleaning Process
Read Part Two - The Carding and Combing Process
Read Part Three - The Spinning Process
Read Part Four - The Weaving Process
Read Part Five - The Finishing Process
However, this isn’t the end! In our next blog post, we’ll be looking at all the things that can go wrong with the product when they are in day-to-day use.